Gold flotation is a technology that utilizes the interaction between the surface of gold minerals and flotation reagents to separate gold minerals from waste ore by causing them to float to the surface of the pulp. As a crucial gold ore beneficiation technique, flotation efficiency directly determines gold recovery rates and consequently impacts the economic benefits of mining operations. To enhance the gold flotation efficiency, it is essential to thoroughly understand the various influencing factors and optimize processes based on ore characteristics, flotation equipment performance, and control of process parameters. The following are four primary factors affecting the gold flotation efficiency.
The influence of ore particle size on gold flotation
The coarseness of ore particle size determines the contact degree between gold ore and flotation reagent, and also affects the adhesion ability between mineral and bubble. Therefore, optimizing ore particle size is the key to improving flotation efficiency.
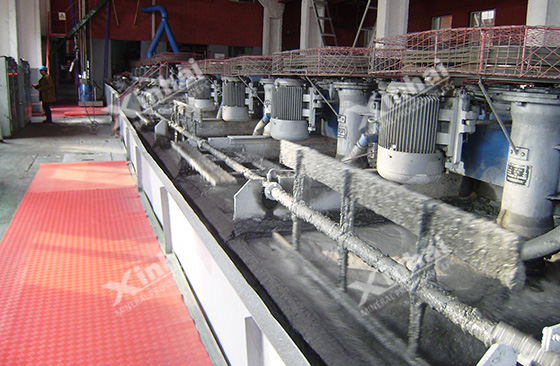
1. The surface of gold ore in overly coarse ore particles is not fully exposed, and flotation reagents are difficult to fully contact with ore, thus affecting the flotation effect. During the flotation process, ore particles need to collide and combine with bubbles to be effectively brought into the flotation foam. If the ore particles are too coarse, the contact opportunity between bubbles and ore particles will be reduced, and the flotation effect will naturally decrease.
2. Overly fine ore particles will be affected by surface charge and hydration film, making it difficult to attach to bubbles, reducing flotation efficiency. Therefore, overly fine ore particles not only increase the viscosity of the slurry, but also lead to waste of reagents.
In order to ensure the maximization of flotation efficiency, reasonable grinding fineness is particularly important. According to the characteristics of different ores, it is generally recommended to control the grinding fineness within the range of -0.074 mm, accounting for 70%-80%. This can ensure the effective recovery of gold minerals without making the ore particles too fine and affecting the flotation efficiency.
Effect of reagent type and dosage on gold flotation
The selection of flotation reagent type and its dosage directly affect the efficiency of the flotation process and the recovery rate of gold minerals. Gold flotation reagents mainly include collectors, frothers and regulators, and their roles in flotation are different.
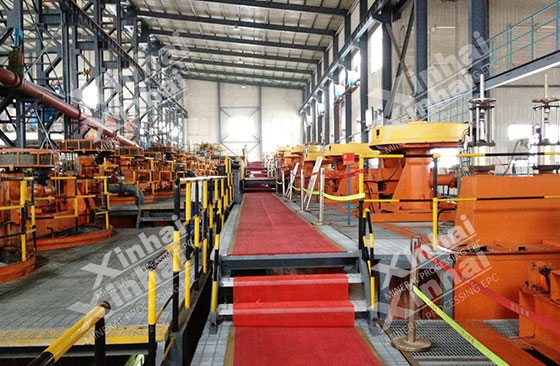
1. Collectors can enhance the hydrophobicity of the surface of gold minerals, allowing gold minerals to combine with bubbles more easily. Common collectors include xanthates, amines, fatty acids, etc. Different types of collectors are suitable for different types of ores. Xanthate collectors are commonly used in the flotation of sulfide gold ores. This type of collector can effectively react with sulfide minerals to improve the flotation of gold minerals. The flotation of oxidized gold ores requires a copper sulfate activator to enhance the floatability of gold minerals.
2. Frothing agents can improve the stability of bubbles during flotation. Stable bubbles can provide a larger flotation area, increase the contact opportunities between ore particles and bubbles, and thus improve flotation efficiency. There are also many types of frothers, and commonly used ones include alkyl sulfonates and aromatic compounds. Choosing a suitable frother can not only effectively improve the stability of bubbles, but also improve the distribution of bubbles in the pulp and promote the flotation of gold minerals.
3. The main function of the adjuster is to adjust the pH value of the pulp and the ion concentration in the pulp, so as to optimize the flotation environment and improve the activity of the agent. Adjusters usually include lime, sulfuric acid, ammonia water, etc. These substances can change the surface charge properties of minerals by adjusting the pH value of the pulp, making it easier for flotation agents to adsorb on the surface of minerals, thereby improving flotation efficiency.
4. The control of the amount of reagents needs to be reasonably configured according to the properties of the ore and the requirements of the flotation equipment, and should also be appropriately adjusted according to the flotation process at different stages. In the flotation process, excessive use of reagents will lead to waste of reagents and increase production costs; too small a dosage will affect the flotation effect and reduce the recovery rate of gold. Therefore, reasonable control of the amount of reagents can improve flotation efficiency and reduce costs.
Gold flotation pulp concentration
The pulp concentration directly affects the collision probability between ore particles and bubbles and the fluidity of the pulp. Too high or too low pulp concentration will affect the flotation effect, so it is crucial to reasonably control the pulp concentration.
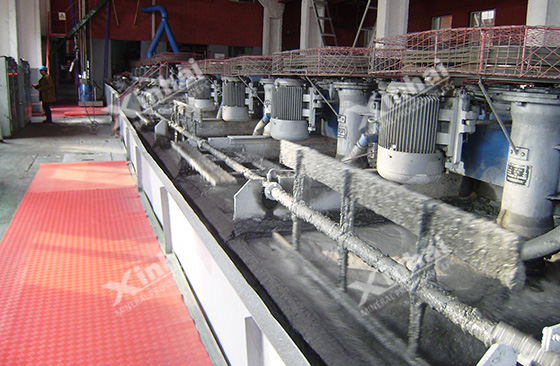
1. When the pulp concentration is too high, the mutual collision between ore particles increases, which easily leads to the sedimentation of ore particles, thereby reducing the collision probability between bubbles and ore particles. In this case, the bubbles cannot effectively combine with the ore particles, resulting in a significant decrease in the flotation effect. In addition, too high a concentration will also increase the viscosity of the ore pulp, affecting the processing capacity of the flotation equipment. Therefore, in the roughing stage, the pulp concentration is usually recommended to be controlled between 30%-40%.
2. Too low a pulp concentration will increase the time required for flotation, thereby reducing the processing capacity of the equipment. Although low concentration can avoid the sedimentation of ore particles, too low a pulp concentration will reduce the efficiency of the flotation process and increase the load of the equipment, thereby reducing the overall flotation efficiency. Therefore, in the selection and scavenging stages, the pulp concentration can be appropriately reduced, but it also needs to be avoided from being too low.
3. Optimizing the pulp concentration requires adjustment based on the characteristics of the ore and the performance of the flotation equipment. By controlling the pulp concentration, the flotation process can be efficiently carried out, the recovery rate of gold minerals can be improved, and the processing capacity of the equipment can be improved.
pH value of gold flotation pulp
The pH value of the pulp affects the activity of the flotation reagent and the flotation properties of the mineral. Different reagents have optimal activity in different pH ranges, so adjusting the pH value of the pulp is an effective means to improve flotation efficiency.
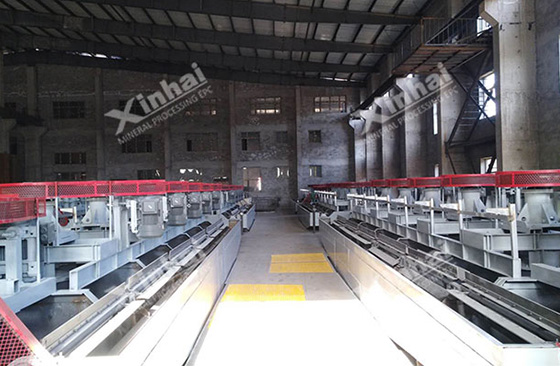
1. Activity of collector: Xanthate collectors work best in weakly acidic to neutral environments, while amine collectors perform better in alkaline environments. Therefore, adjusting the pH value of the pulp to make it suitable for the collector used can significantly improve the flotation efficiency.
2. Flotation properties of minerals: Because the pH value of the pulp changes, the surface charge of the mineral will change, which in turn affects the interaction between the mineral and the flotation reagent. Some minerals are positively charged in an acidic environment and negatively charged in an alkaline environment, which will affect the adsorption of the flotation reagent and the flotation effect of the mineral.
3. Adjustment of pH value: By adding adjusters such as lime and sulfuric acid, the pH value of the pulp can be adjusted to the optimal range suitable for flotation, thereby improving the recovery rate and flotation efficiency of gold minerals.
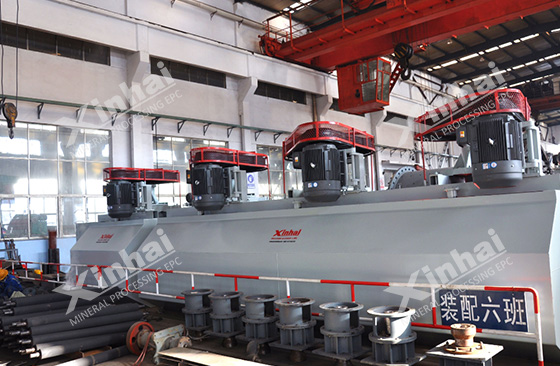
The gold flotation efficiency is affected by many factors, among which ore particle size, reagent type and dosage, pulp concentration and pH value are the most critical factors. Reasonable control of these factors can significantly improve the flotation effect, ensure the efficient recovery of gold ore, optimize the flotation process, and improve the overall efficiency of gold ore dressing. By deeply studying the characteristics of ore and the mechanism of action of flotation reagents, optimizing the flotation process can not only improve the flotation recovery rate, but also effectively reduce production costs and improve the economic benefits of mines.
Tags:Gold Flotation
From:Xinhai Mining Machinery Company