In the grinding operation, the consumption of steel ball is very large, which is about 10 times more than the loss of ball mill liner. In order to make up for the loss of steel ball and keep the size of the steel ball unchanged in the ball mill machine, it is necessary to add the steel ball regularly according to a certain ratio.
The consumption of steel ball in the ball mill machine is mainly caused by mechanical wear and corrosion wear, which are the irreversible “physical-mechanical process” and “physical-chemical process” on the solid surface. So how to effectively reduce the energy consumption of steel ball on the premise of guaranteeing the quality of grinding quality of ball mill machine?
1. Change the grindability of the ore
The grindability of feed material to the ball mill machine is one of the reasons that affect the energy consumption of steel ball. Generally, if the grindability of the feed material is small, the ore is easy to grind, the wear of steel ball in the ball mill machine is low, and the consumption of steel ball in the ball mill machine is low.
In the actual production, if the ore is difficult to grind or the ore requires the fine grinding, adding a certain chemical reagent in the grinding process can improve the grinding effect and increase the grinding efficiency if the economic and site conditions allow. Besides, heating the ore can change the mechanical properties of the whole ore, reduce the hardness of the mineral. These two methods can effectively reduce the energy consumption of the ball mill machine.
2. Reduce the feed size
If the feed size of the ball mill machine is large, the work of the ball mill machine on the material is also larger. In order to reach the specified grinding fineness, the workload of the ball mill machine is bound to increase, and the energy consumption of the steel ball will be increased correspondingly.
In order to reduce the power consumption of the ball mill machine, the feed size can be reduced. Therefore, the particle size of the crushing product is required to be small, that is, “more crushing and less grinding”.
3. Control the filling rate of steel ball
When the rotation speed of the ball mill machine reaches a certain degree, the filling rate is large, and the impacting times of steel ball on the material are more, the grinding area is large and the wear is fast. In addition, the too-high filling rate will change the movement state of the steel ball in the ball mill machine, reduce the impact effect on the large particle material. On the contrary, if the filling rate is too small, the grinding effect is weak.
At present, the filling rate of steel ball in the grid type ball mill is 45%~50%, and the filling rate of steel ball in the overflow type ball mill is 38%~42%. Of course, the mentioned are not reasonable filling rates for all mineral processing plants. The ball load should be determined according to the mineral processing test.
4. Control the size and ratio of steel ball
The steel ball in the ball mill machine and the material is point-to-point contact. If the diameter of the steel ball is too large, the crushing force is large, which will lead to excessive wear, and the material break along the direction of penetration force, thus affecting the grinding efficiency.
In addition, under the same filling rate of steel balls, the individual number of steel balls will be less if the ball diameter is too large, the probability of crushing is low, so the over-crushing phenomenon will be intensified, and the product granularity will be uneven. The too-small steel ball has a small crushing force on the ore, and the grinding efficiency is low. Therefore, the reasonable size and ratio of steel ball can not only reduce the consumption of steel ball in the ball mill machine, but also effectively improve the grinding efficiency.
5. Control grinding concentration
The grinding concentration will affect the specific gravity of the pulp, the adhesion of the material around the steel ball and the fluidity of the pulp. If the grinding concentration is appropriate, the adhesive degree of the material around the steel ball is good, the impact and grinding effect of the steel ball on the material are also great, so the steel ball wears fast.
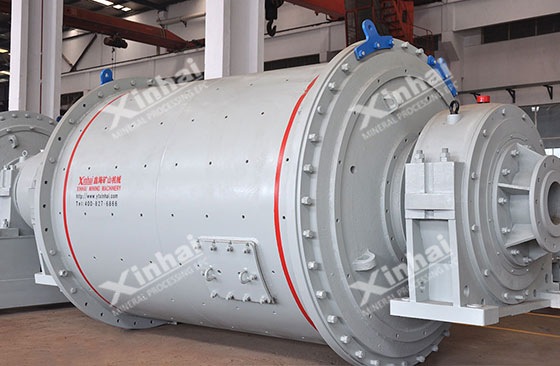
In actual production, the grinding concentration can be controlled by controlling the amount of ore feed, water supply, or adjusting the classifying function.
6. Control the rotate speed of ball mill machine
On the premise of reasonable steel ball ratio of ball mill machine, the steel ball inside the cylinder will be thrown down, rather than falling with the increasing of the rotate speed of ball mill machine. When the rotation rate is increased to a certain level, the useful power will reach the upper limit. At this time, the grinding effect is better and the wear of the ball mill machine is also reasonable.
The theoretical critical speed of ball mill machine is generally 78%~ 85%. Due to the nature of materials and other factors, the rotate speed of the ball mill machine should be determined according to the actual situation.
In addition, the quality of the steel ball will affect the productivity and the consumption of steel ball, thus affecting the grinding cost. When choosing the steel ball, the steel ball has its proper hardness value. if only consider the consumption of steel ball, the higher the hardness is, the lower consumption is. But for the productivity of the ball mill machine, the productivity will increase with the increasing ball hardness under a certain range, but once the hardness is over a certain range, the productivity of the ball mill machine will be decreased, and the steel ball is fragile. Moreover, the density of the steel ball is also a problem that cannot be ignored.
There are many factors affecting the energy consumption of steel ball in the grinding process, and most of the factors are difficult to make quantitative analysis, which can only be qualitatively analyzed. In order to reduce the power consumption of steel ball under the premise of guaranteeing the quality of reasonable index, we must consider it from the multiple links, and control each link to achieve the good technical and economic indexes.
Usage scenario of Xinhai ball mill machine
1. Guinea 8000tpd gold ore processing plant
2. Uganda 720tpd phosphate ore processing plant
3. Malaysia 700tpd gold ore processing plant
4. Morocco 500tpd silver ore processing plant
5. Russia 500tpd gold ore processing plant
6. Pakistan 1500tpd copper ore processing plant
7.Vietnam 800tpd graphite ore processing plant
8. Zimbabwe 700tpd gold ore processing plant
Tags:Xinhai, exhibition
From:Xinhai Mining Machinery Company